Have you ever wondered what stands between your ceramic coffee mug and a potential crack? The answer lies in the ceramic’s hardness, a crucial metric that impacts both consumer and industrial applications.
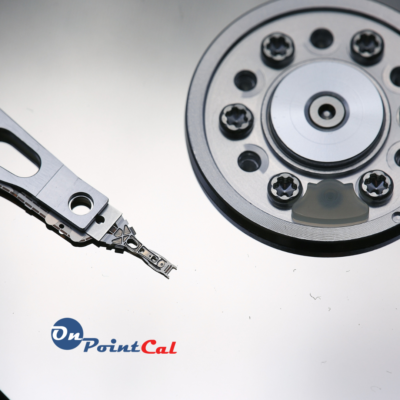
Deciphering the Role of Hardness in Ceramics
- Longevity and Durability: The harder the ceramic, the better it resists scratches and abrasions. This means a prolonged service life and a product that retains its aesthetics and functionality.
- Thermal Strain Resistance: Especially relevant for ceramics in the aerospace and automotive sectors. The hardness determines a ceramic’s ability to withstand temperature variations without developing cracks.
- Environmental Strain Resilience: From UV rays to chemicals, ceramics face numerous environmental challenges. Their hardness plays a significant role in combatting these factors, ensuring product integrity.
- Mechanical Load Bearing: The hardness of ceramics signifies their capacity to endure mechanical stresses, determining if they will deform or stay intact.
Why Calibration Laboratories are the Unsung Heroes
True hardness testing isn’t just about the equipment but its calibration. Consistent, precise results are paramount, and that’s where ISO 17025 calibration laboratories shine. By ensuring optimal performance of hardness testers, these labs play a pivotal role in safeguarding the quality of ceramic components across industries.
B2B Implications: The Assurance of Quality
For businesses and testing labs delving into ceramics, calibrated hardness testing is more than a routine—it’s a mark of quality assurance. By aligning with ISO 17025-certified labs, they emphasize their commitment to excellence.
Conclusion
Ceramics are versatile, resilient, and indispensable. By prioritizing calibrated hardness testing, we not only ensure their quality but also their longevity and dependability, be it in a consumer or industrial setting.